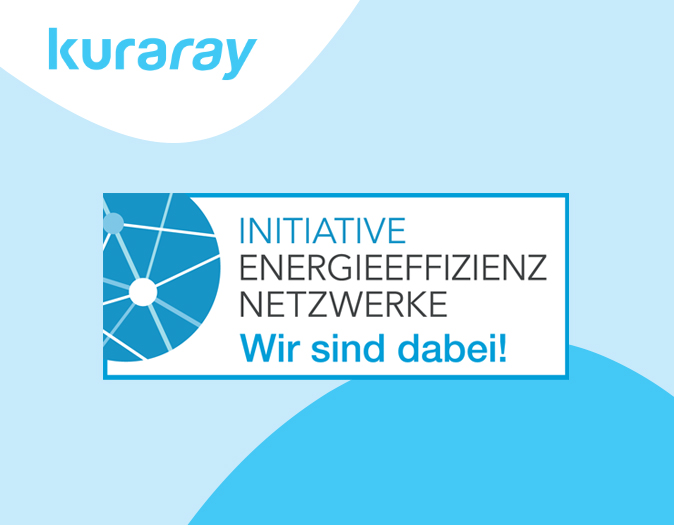
Kuraray raises energy efficiency by 16 percent
Industry plays a key role in meeting the German government’s climate targets. Kuraray, a leading manufacturer of speciality chemicals, is aware of its responsibility and works continuously to optimise energy efficiency and reduce CO2 emissions at its production sites at Höchst Industrial Park in Frankfurt am Main and in Troisdorf. Kuraray is now sharing its experience in the third Rhine-Main Energy Efficiency Network and has been granted the AGEEN quality seal for its commitment. Intelligent process control, heat integration in solvent recovery and innovations in the transport of materials have brought a substantial improvement in energy efficiency of up to 16 percent at Kuraray’s production lines in Frankfurt since 2011.
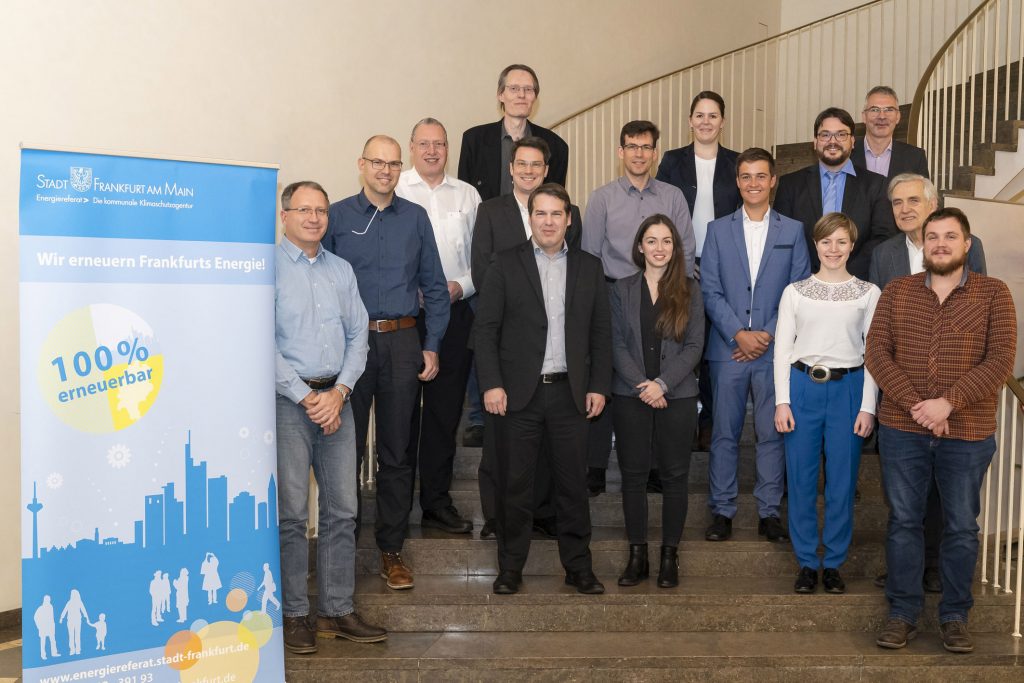
“As a leading speciality chemicals producer, making sure we respect the environment is very important to Kuraray. Therefore, we constantly strive to optimise energy consumption and emissions at our sites,” says Dr. Jörg Schappel, Head of Leiter QHSE & Product Stewardship at Kuraray in Europe. “In the Rhine-Main Energy Efficiency Network, we can share our experience with other companies in the region and work together to make our activities more sustainable and environment-friendly.” The network was initiated by the City of Frankfurt’s energy department. Alongside Kuraray, there are six other members – including Lufthansa subsidiary LSGG Sky Chefs, Infraserv Höchst and pharmaceuticals manufacturer Sanofi-Aventis. As a network partner, Kuraray has now been awarded the AGEEN quality seal. This seal of approval is awarded by AGEEN, the German association of energy efficiency networks, to companies that work towards more efficient use of energy resources.
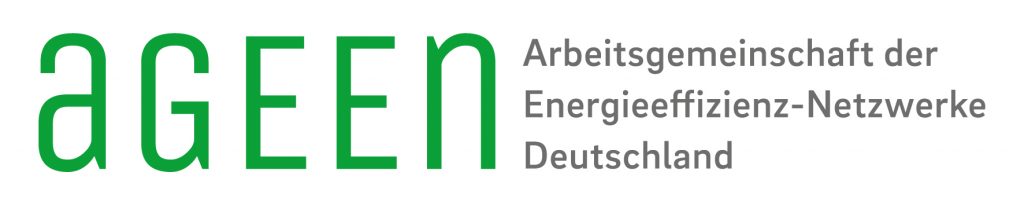
A strong tool and an interdisciplinary team for energy-saving processes
Kuraray has already made good progress in energy efficiency. One major milestone was the introduction of an ISO 50001-compliant integrated energy management system in 2013. A key element is an interdisciplinary team of experts from management, production, and the process control, process technology and controlling departments. This team works on solutions to enhance energy efficiency at the production sites. “Our energy management system is an effective tool to help us move continuously towards climate-neutrality,” says Dr. Jörg Schappel. “Steadily improving our processes is an important area of focus.”
Optimising processes, leveraging potential
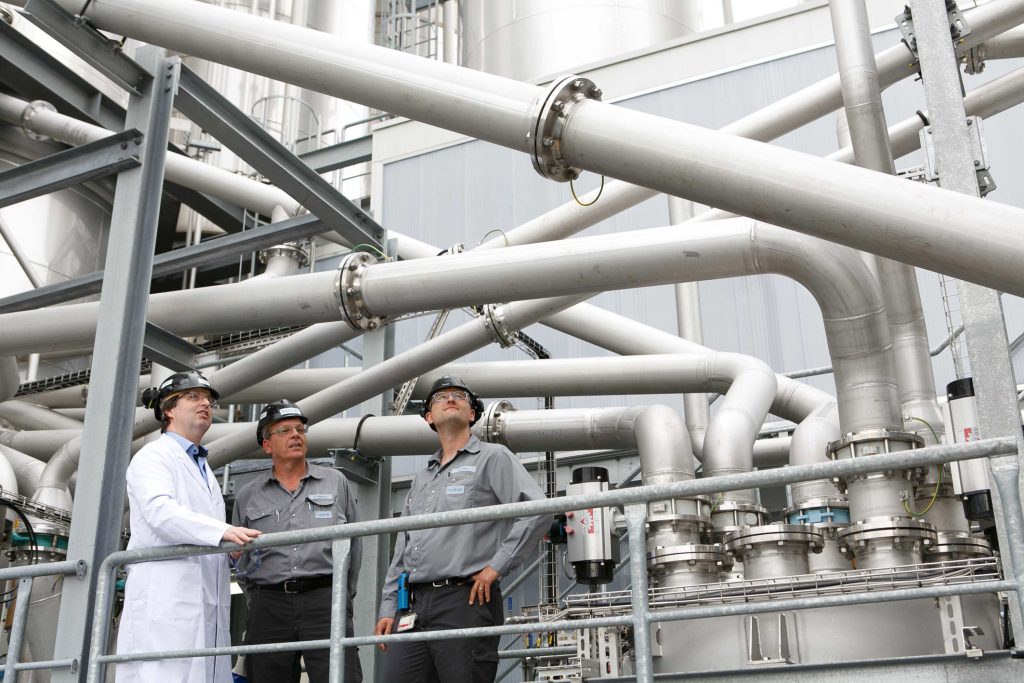
One example is distillation, which is used to recover solvents from production processes. Optimum regulation of the distillation process used to separate substances has brought a noticeable reduction in energy consumption. Moreover, intelligent integration of heat enables the facility to convert 70 percent of primary energy sources into secondary energy for use in other process steps. Another project is a pneumatic conveyor system in pipes at the Frankfurt-Höchst site to transport powder and granulates from production plants to the silos used for interim storage and to filling stations. Better networking of the compressors that generate the necessary pressure means that Kuraray can regulate the system in line with need, resulting in a significant reduction in energy consumption.
“Process improvements and technical innovations have improved the energy efficiency of the production of Mowital® polyvinyl butyral in Frankfurt by 14 percent on the past eight years. And in the production of KURARAY POVAL™ polyvinyl alcohol, we have improved energy efficiency by 16 percent,” reports Dr. Jörg Schappel. “We want to build on this success and work with our partners in the energy efficiency network and with the City of Frankfurt’s energy department to achieve our goal of making Frankfurt climate-neutral by 2050.”