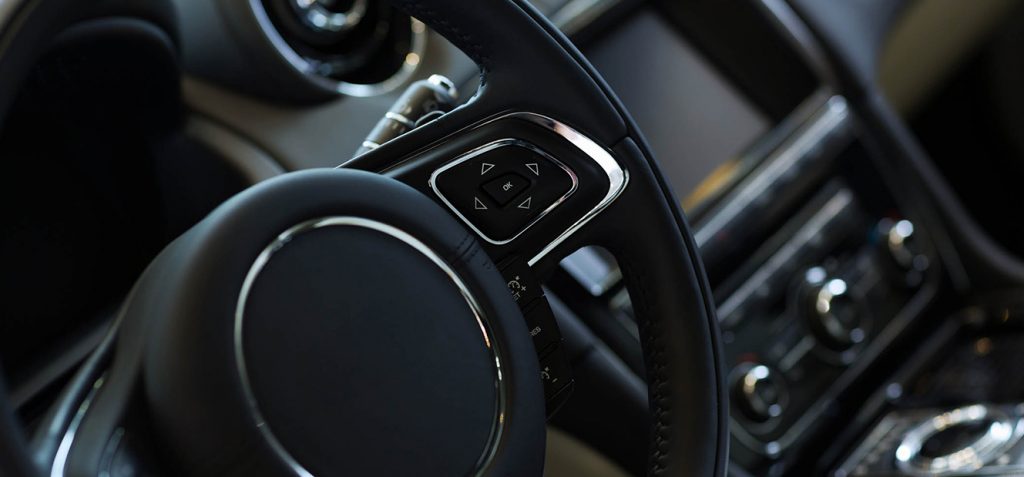
Triblock copolymer HYBRAR™ damps noise and vibration in vehicles
E-mobility and vehicle weight reduction are two central trends in automotive engineering. In vehicle design, noise reduction is also playing a key role. This is because the lower noise level of electric motors makes annoying rattling and squeaking noises more audible. In addition, the lightweight plastics parts used today can be a source of new unpleasant noises. The prevention of noise and vibration calls for materials that achieve high damping performance over a wide frequency range while being easy to process. HYBRAR™ is a highly elastic triblock copolymer with unique damping properties that can be flexibly processed in combination with various other materials such as polypropylene, polyamide, and polycarbonate.
High Vinyl Content for Outstanding Damping and Incredible Stability
HYBRAR™ is a styrene block copolymer (SBC) with a poly-diene block featuring a high vinyl content. Thanks to its special structure, the material achieves its maximal damping effect close to room temperature – ideal for use in reducing noise in vehicles and in industry. Compared to conventional styrene block copolymers, HYBRAR™ shows a significantly higher peak tan delta. In addition, it covers a wider frequency range – from very low frequencies, such as the resonance of the body, to very high frequencies, such as that of rubbing glass components. With these properties, it is ideal for absorbing various kinds of noise and vibration in vehicles.
HYBRAR™ can be processed into a wide variety of forms, including films, tubes and injection molding. HYBRAR™ is resistant to heat and the effects of the weather for hydrogenated form, and is highly compatible with applications in challenging environments, e.g. in vehicle engine compartments. Available in hydrogenated and non-hydrogenated forms, the hydrogenated grades show excellent miscibility with polypropylene (PP), achieving a blend with a considerably finer dispersion than conventional SBC – for greater transparency, flexibility, stability, and improved impact strength. Adding only 30 percent HYBRAR™ to polypropylene improves tan d peak intensity at room temperature by some 80 percent. This means, for instance, that effective damping applications can be implemented at low cost compared to composite materials.
Versatile in Its Uses – from Protective Covers to Engine Components
The plasticizer-free processing of HYBRAR™ is extremely environment-friendly and permits a wide range of techniques such as film and profile extrusion as well as maximum flexibility in injection molding. In the automotive industry the material is already in use in combination with polypropylene, e.g. in shock absorbers, instrument panels, and door trim. Owing to its outstanding mixing properties, such as with high-density polyethylene (HDPE), ethylene propylene diene monomer rubber (EPDM), polycarbonate (PC), and polyamide, HYBRAR™ is also ideal for applications such as covers, gasket rubber, radiator grilles, and engine compartment parts.
Various Other Applications – from Tool Grips to Sports Shoes
In addition to the automotive sector, various other industries are already benefiting from the outstanding properties of HYBRAR™. It damps sports equipment, tool grips, loudspeaker cones and boxes, shoe soles, and floorcoverings. In addition, the triblock copolymer is utilized as a damping modifier in various thermoplastics and rubbers. HYBRAR™ can be used as a key component of adhesive and sealant applications such as adhesive tapes and industrial and construction adhesives. HYBRAR™ imparts impressive flexibility and elasticity to food and industrial packaging, and in the medical sector it replaces natural rubber, latex, and PVC in such items as elastic hygiene components and medical films and tubes.