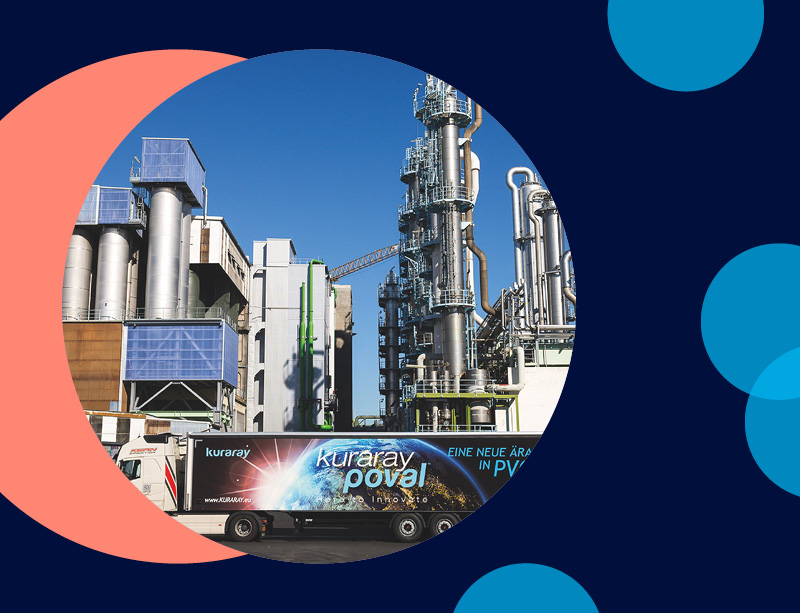
Anniversary of the Kuraray Poval™ production plant in Frankfurt
The Poval plant in Höchst Industrial Park is big, complex, diverse and unbelievably important for our business. This year marks its 50th anniversary. Kuraray Poval™ polyvinyl alcohols (PVOH/PVA) have been produced here since 1971. Thanks to a wide range of optimizations and process improvements, the Poval plant is now a benchmark for energy efficiency in the Kuraray Group. To make sure that our customers can continue to use the benefits of Kuraray’s ‘champion of versatility’ in their PVA applications in the next 50 years, the plant has been aligned optimally for future requirements. It is therefore well-prepared for the upcoming challenges.
Kuraray Poval™ polyvinyl alcohols (PVOH/PVA) are key starting products in many industries – from the production of speciality papers, PVC plastics, food packaging, textiles, cosmetics and ceramics to construction materials, emulsions and adhesives. Another feature has always been the extremely wide range of applications for the various PVA grades. Their unique properties improve product quality and performance as well as production efficiency. Moreover, their very good environmental compatibility and health profile facilitate the development of sustainable solutions, for example, as auxiliaries in the production of paper, as textile sizes, in the production of dispersions and as barrier films. PVA has high bonding power, excellent film-forming properties and very good barrier properties. It is also water-soluble, recyclable and is not a health hazard. Such properties are an excellent starting point for an increasingly wide range of innovative and sustainable applications such as water-soluble laundry bags for hospitals, detergent pods, 3D printing and the food, beverage, healthcare and cosmetics industries.
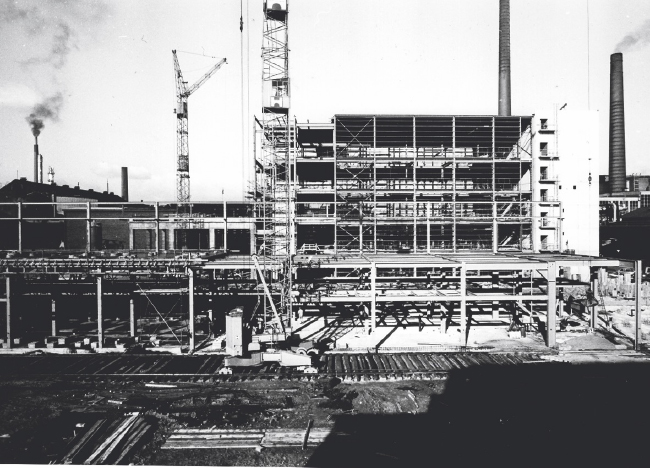
This versatile product has been produced in Europe in Kuraray’s Poval plant in Frankfurt-Höchst/Germany for 50 years. Production started on three lines in 1971 and the PVA was originally marketed as Mowiol. Back then, the plant was operated by Hoechst AG and was one of the largest at Hoechst’s main site in Frankfurt. To this day, the hallmarks of the plant are its complexity and highly networked processes.
The start of a new era with Kuraray
The acquisition by Kuraray Co., Ltd. in 2001 opened many doors for the Poval plant. Plans to extend the plant, which had been on hold, were implemented and in the following years Kuraray undertook extensive modernization of the production facilities (Lines 5 and 6), the control room, lab, tank farm and filling facilities. Today the plant is well-prepared for the upcoming challenges.
Kuraray Poval™ is a sought-after product: production capacity has therefore been increased significantly over the past 50 years. Start-up of further production lines (in 1978, 2005 and 2014) and various projects to optimize process control, along with debottlenecking of parts of the plant, have increased output 3.5-fold since the start of production. Output is not just sold to external customers: a high proportion goes to internal customers. From the beginning, most of the production has been channelled to the adjacent plant as an aqueous solution where it is used to produce the Mowital brand of PVB. For many years, PVA from Frankfurt-Höchst has also been used in the manufacture of water-soluble MonoSol films in the USA and the UK.
Major goals: optimizing quality and energy consumption
Product quality and production volumes depend on many different parameters. Since the 1990s, constant efforts have been made to adapt the production process to reduce specific energy costs. Matthias Gutweiler, now Managing Director of KEG, was manager of what was then the Mowiol plant from 1996 until 2002. He recalls: “High price pressure on the market in the 1990s and 2000s increased the need to improve productivity and the production efficiency.”
A key step towards increasing efficiency and saving energy was the conversion of the distillation column for the mother lye in 2013 (MoWES project) and the optimization work is still ongoing. because quality and energy consumption (steam per tonne PVA) can be influenced by how the production facilities are operated and the dynamic processes in the distillation unit.
In terms of energy efficiency, the Poval plant is now a benchmark within the Kuraray Group.
Dr. Matthias Gutweiler, Managing Director of KEG
Safety has top priority
The large number of integrated process steps makes working in the Poval plant very demanding. Safety also has very high priority. The plant safety, occupational safety and environmental protection requirements defined by the relevant authorities have to be observed. The responsible members of the plant team work through all necessary steps and activities and document them systematically with external support. “Regular training, safety talks and individual e-learning modules for employees are now common practice,” explains Michael Giebisch, who was plant manager for ten years and is now operations manager responsible for all 105 employees in production, engineering, ESHA, quality control and logistics. They all work together on the continuous improvement of our PVA products, focusing on sustainability and the future.
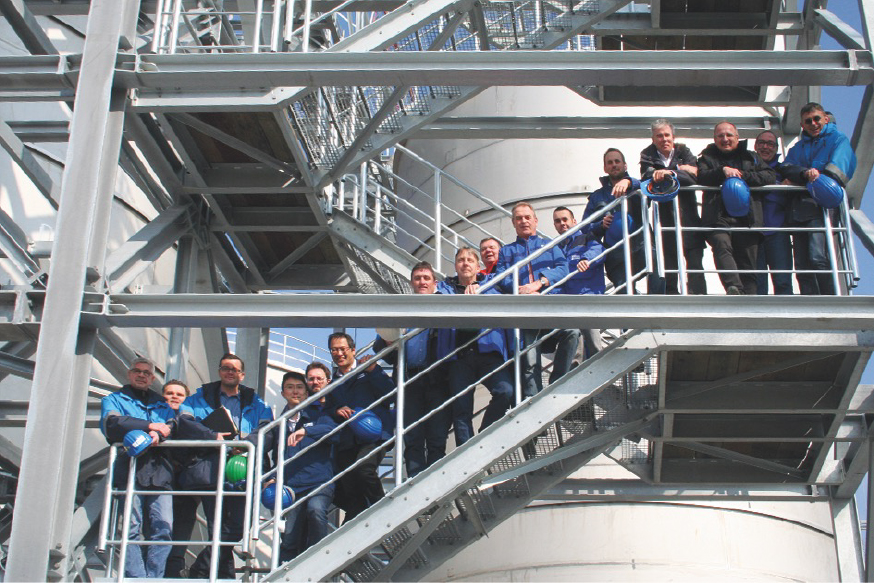
Focus on the future: production of Exceval™ and specialities
“The Poval plant is making good progress,” says Christian Müller, who has managed the Poval plant since 2017. “It’s important for us that all teams pull together and work for the future of the plant.” The focus on process improvements and the introduction of state-of-the-art digital process control applications, which the process engineering team has been working on since 2017, have paid off: there has been a significant improvement in quality indicators and capacity utilization.
Validation of the PVA products as conforming to GMP (good manufacturing practice) means Kuraray can now also do business with demanding customers in the cosmetic and animal feed industries. Further specialities and new technologies such as the production of the copolymer Exceval™ give the plant good prospects for the next 50 years.